Part of what makes the Touchstone family so unique is that we have our own amazing hold manufacturers, Stone Age Climbing Holds. Stone Age gives us the flexibility to dream up exciting new holds for our walls so that we can always challenge and inspire the climbers who come visit our gyms. A couple weeks ago, Andrea Laue of Climbing Magazine took a peek at how the magic happens in our Sacramento facility and has the photos to prove it! Below is an excerpt from Andrea’s step-by-step tour of Stone Age’s process.
Modern climbing gyms are works of art, and the holds adorning the walls are the stars of the show. Stone Age, the hold supplier for Touchstone climbing gyms, gives us a behind-the-curtain look at how holds are made.
Stage: Shape
Shapers saw blocks of artist’s foam into smaller sizes, then progress from rough to precise cuts using a variety of tools. They may remove large amounts of material to start, but they eliminate less and less foam with each cut as the hold takes shape. Shapes are finished using sandpaper or bare hands. Shapers dial in the final form and feel of the hold, loosely grabbing it how they intend it to be used. Attention is paid to every detail, from the anticipated angle of the climber’s fingers when she grabs the final hold to the edges of the bolt hole.
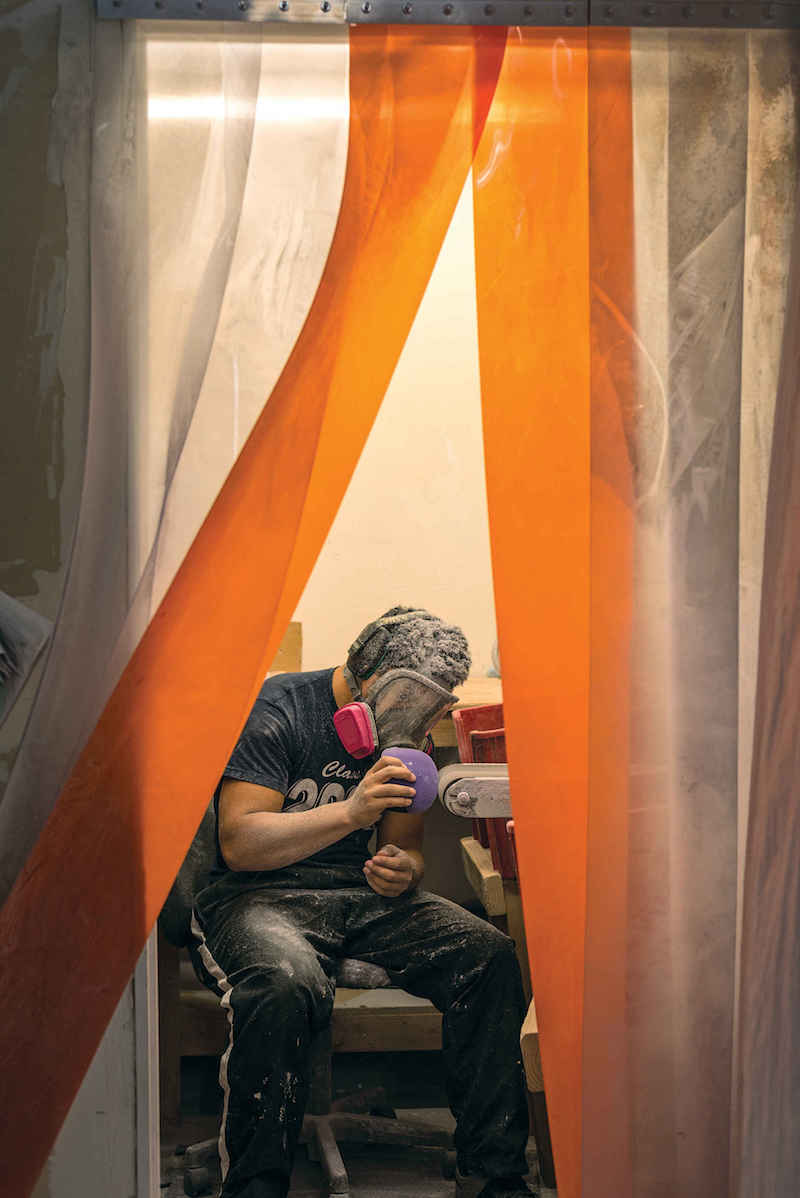
Stage: Mold
Next a mold for the newly shaped hold is framed. Makers will put the shaped hold into the frame and then pour silicone around it which creates a mold. Legos are a colorful and versatile option to create these frames. Mold makers estimate the necessary height of the frame in relation to the size of the holds. Make the mold too thin and it won’t hold up to multiple pourings; make it too thick, and it wastes expensive silicone. As such, a few corners are cut in the final frame to save material. Walls are taped to ensure smooth faces and easy removal.
Be sure the check out the full photo gallery and article here to learn about the rest of the hold-making process.